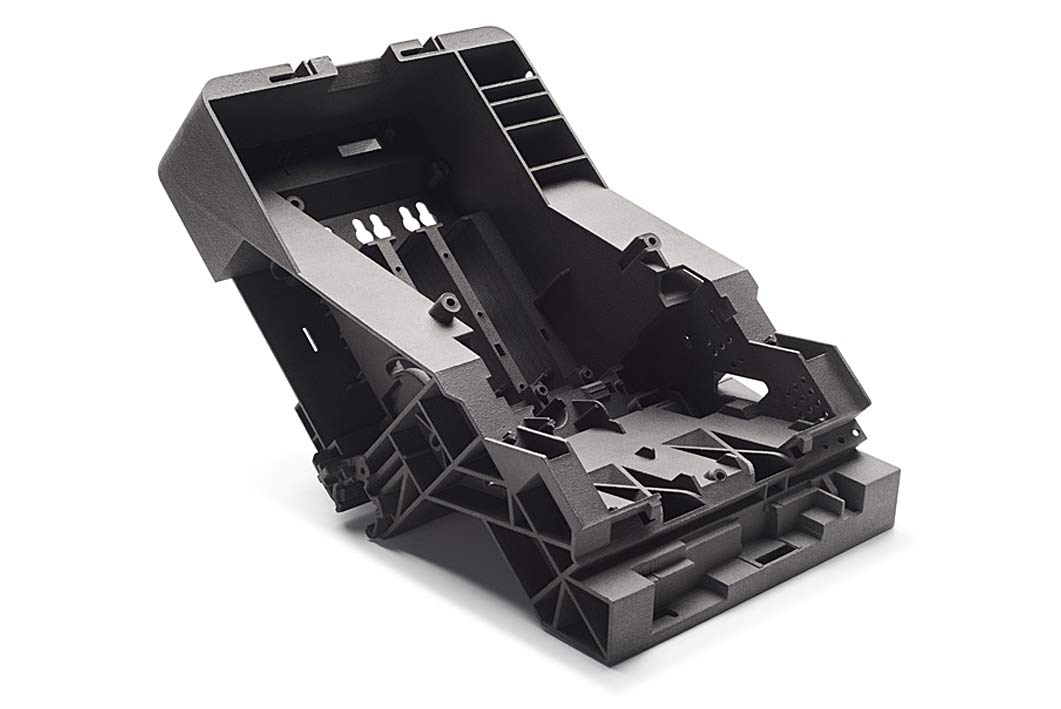
Effiziente Produktion komplexer Baugruppen
Die Additive Fertigung als zukunftsweisendes Herstellungsverfahren
Ob bei der Erstellung von Prototypen oder bei der industriellen Serienproduktion – mit der additiven Fertigung erhalten Baugruppen trotz Komplexität eine gewisse Einfachheit. Durch die Addition des Materials können Bauteile in jeder erdenklichen Form erstellt werden. Die Wertschöpfungskette der Additiven Fertigung findet von der Idee bis zur Oberflächenbehandlung in unserem Hause statt. Dies erlaubt es uns mit der fortschreitenden 3D-Drucktechnik zu wachsen.
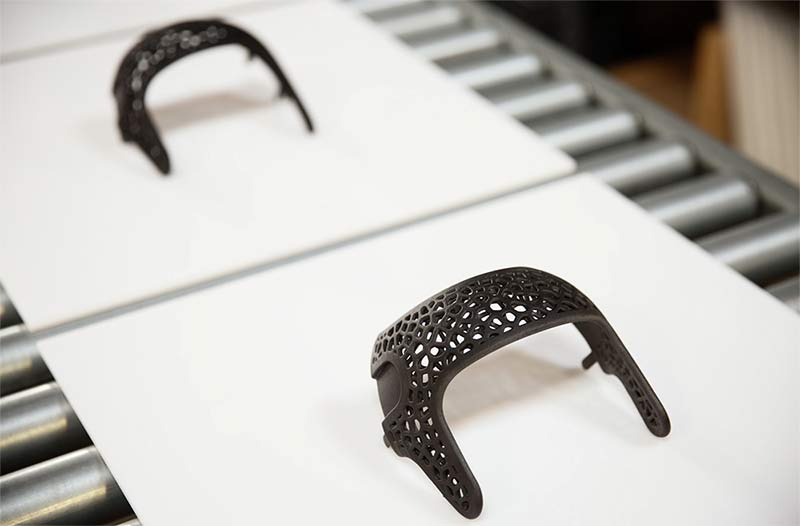
Wir beraten Sie und wählen für Ihre individuellen
Anfragen folgenden Additive Fertigungsverfahren aus
Multi Jet Fusion (MJF)
Das Multi Jet Fusion Verfahren ist ein an das Selektive Lasersintern angelehnte additive Verfahren.
In dem Bauraum wird Schicht für Schicht ein Pulver aufgetragen. Mittels zweier Flüssigkeiten wird der Druckbereich vom Rest des Bauraumes getrennt. Der Auftrag erfolgt ähnlich wie bei einem Tintenstrahldrucker. Die Kunststoffschichten werden mit einer Heizlampe miteinander verschmolzen. Durch den schnellen Auftrag der Flüssigkeiten und der flächendeckenden Einbringung der thermischen Energie, ist das Verfahren bis zu 10mal schneller als andere Verfahren.
Die hohe Produktivität und Maßhaltigkeit, ermöglicht niedrige Stückkosten. Dadurch eignet sich das Verfahren auch bei großen smarten Serienbauteilen.
Anwendungsgebiete:
Gehäuseteile in der Elektronikindustrie
Orthesen für die Medizintechnik
Prototypen im Maschinenbau
Maschinenmodelle für Industrieplaner
Vorteile:
Hohe Präzision
Schneller Prozess
Sehr gute Stabilität der Bauteile
Kein Stützmaterial erforderlich
Hohe Materialdichte
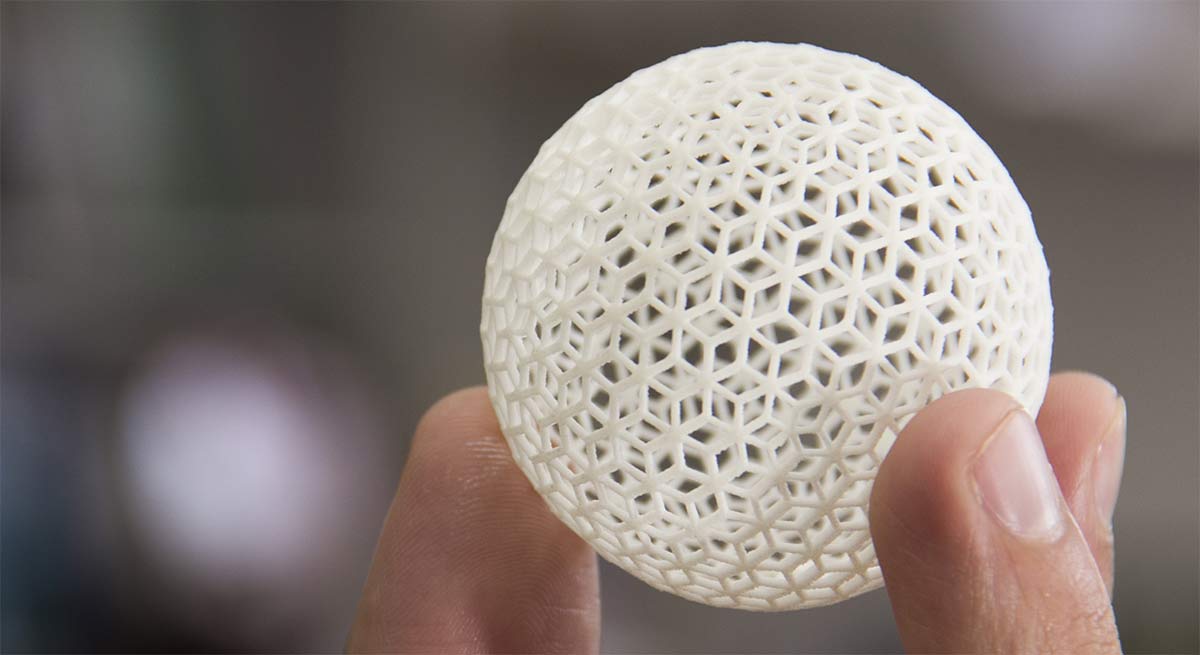
Selektives Laser Sintern (SLS)
Anwendungsgebiete:
Prototypen in der Verpackungstechnik
Baugruppen mit integrierten Funktionen in der Automatisierung
Serienbauteile in der Elektronikindustrie
Anschauungsmodelle für das Bauwesen
Vorteile:
Große Werkstoffauswahl
Kein Stützmaterial erforderlich
Hohe Detailgenauigkeit
Teile sind belastbar
Bei diesem additiven Fertigungsverfahren werden Werkstücke verfahrensbedingt Schicht für Schicht aufgebaut. Mittels Laserstrahl wird ein Kunststoffpulver aufgeschmolzen, anschließend wird eine neue ca. 0,1 mm dicke Schicht Pulver aufgetragen und wieder an den Stellen, wo Material benötigt wird, aufgeschmolzen.
Durch die stützende Wirkung des Pulvers um die Bauteile, kann auf Stützstrukturen verzichtet werden. Des weiteren kann eine sehr komplexe Geometrie, selbst mit Hinterschneidungen, erzeugt werden. Nach dem Drucken werden die Bauteile in der Regel glasperlengestrahlt. Anschließend sind Postprocessings wie: spanende Nachbearbeitung, Glätten, Färben, Beflocken u.v.m. möglich.
Fused Deposition Modeling (FDM)
Bei diesem Herstellungsverfahren wird ein Werkstück schichtweise aus schmelzfähigem Kunststoff aufgebaut. Ein Extruder fördert den Kunststoff zum Heizelement, indem der Werkstoff aufgeschmolzen wird.
Ein zweiachsiges Portal bewegt die Düse, wo der Strang definiert auf der Bauplattform aufgetragen wird. Der Kunststoff kühlt ab und erstarrt. Um komplexe Strukturen herzustellen, kommt Stützmaterial, das später wieder entfernt wird, zum Einsatz.
Anwendungsgebiete:
Prototypen mit Consumer Bereich
Hilfsmittel und Lehren für Montage im Maschinenbau
Auswaschbare Kerne für Formteile aus Carbon für den Rennsport
Leichte Robotergreifer in der Automatisierungsbranche
Vorteile:
Einfacher Prozess
Kostengünstiges Verfahren
Postprocessings wie Lackieren und Glätten möglich
Werkstoffe mit verschiedensten Eigenschaften möglich
In Abhängigkeit des ausgewählten Verfahrens
sind folgenden Materialien möglich
PA 12
PA 12 GF
TPU 91 A
ABS
PLA
Alumide
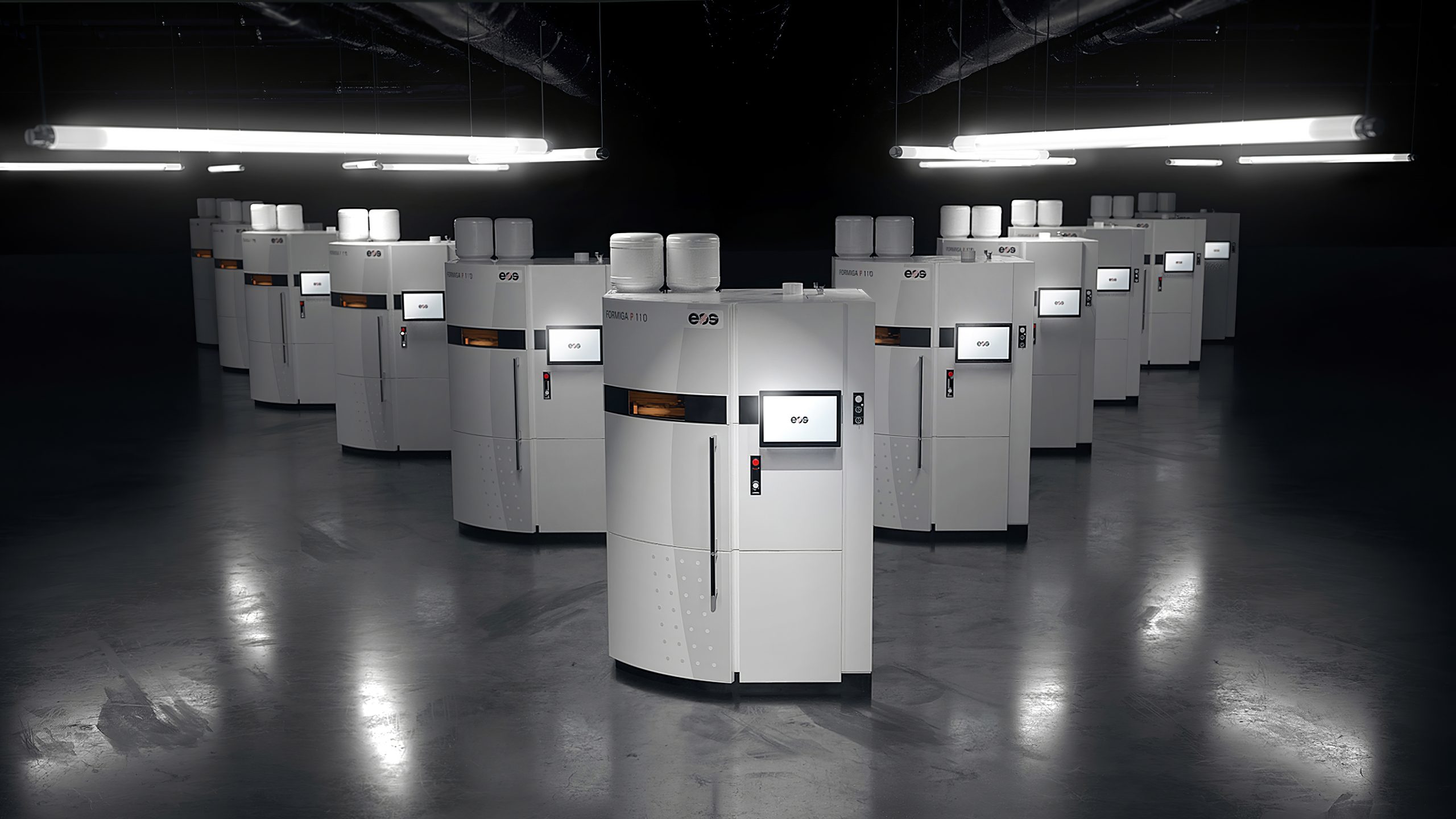
Produktionsbeispiele
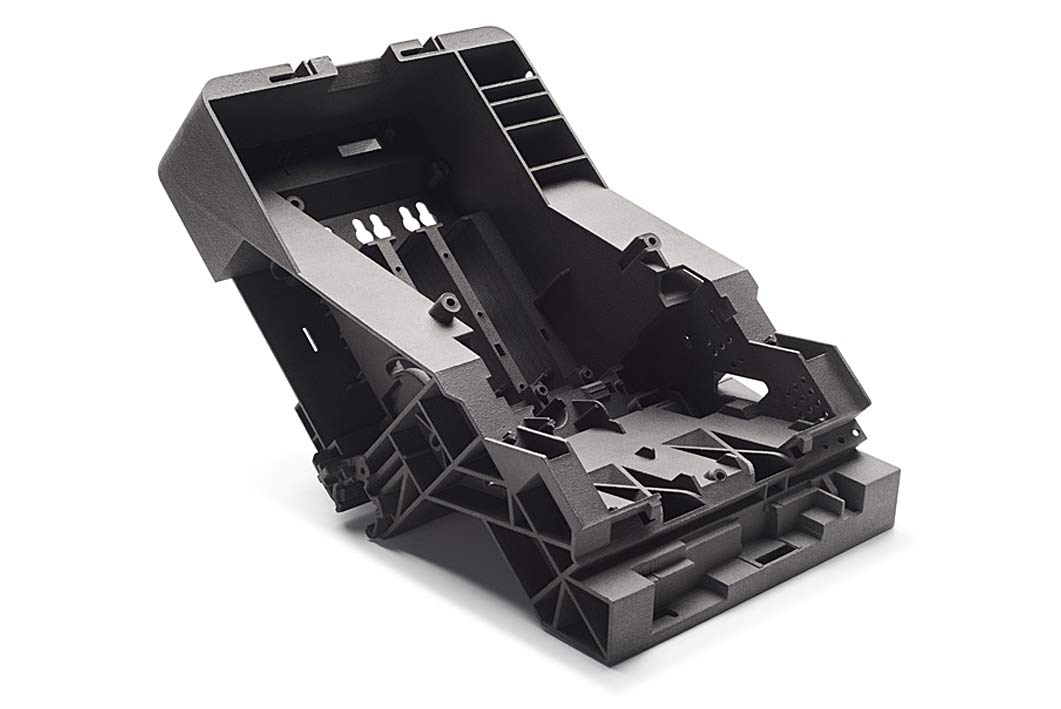
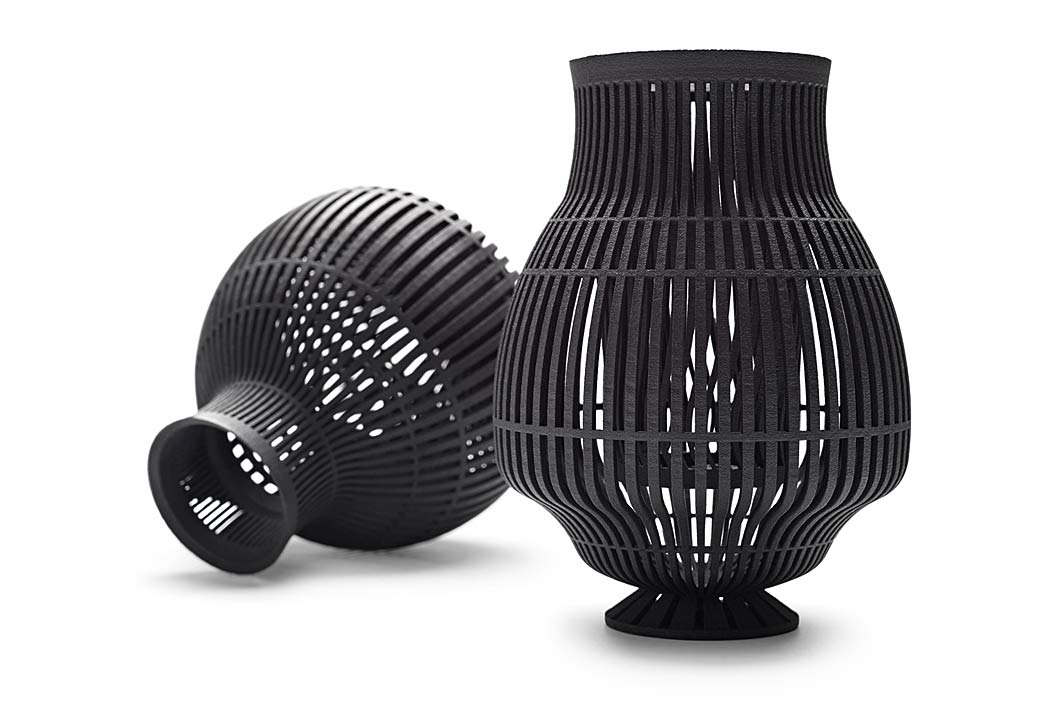
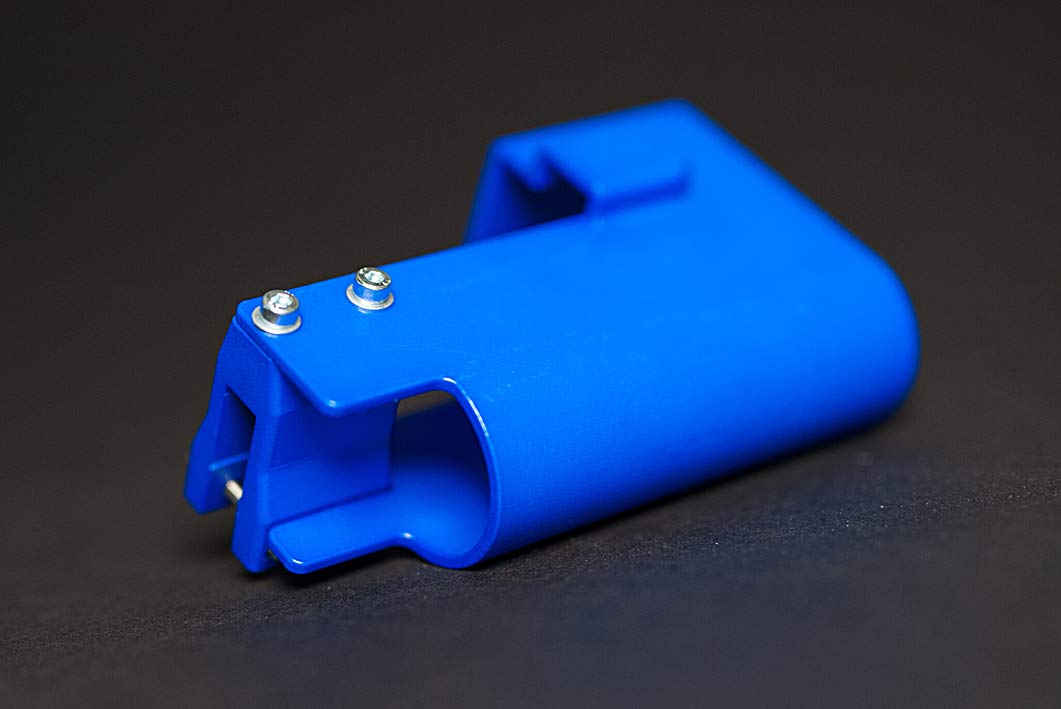
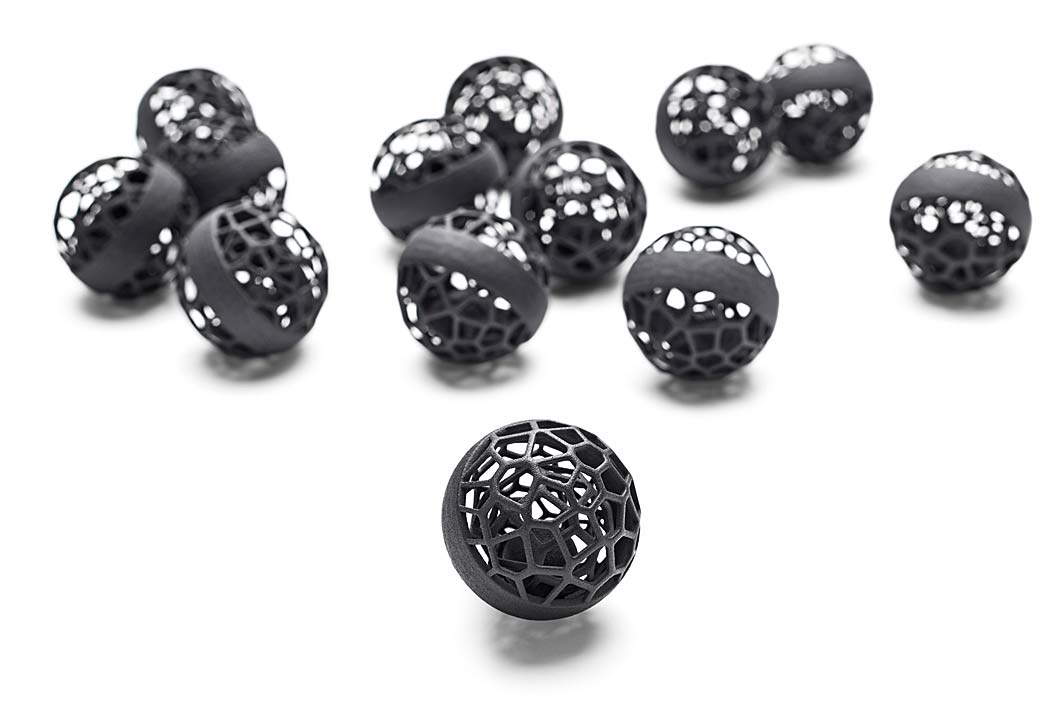
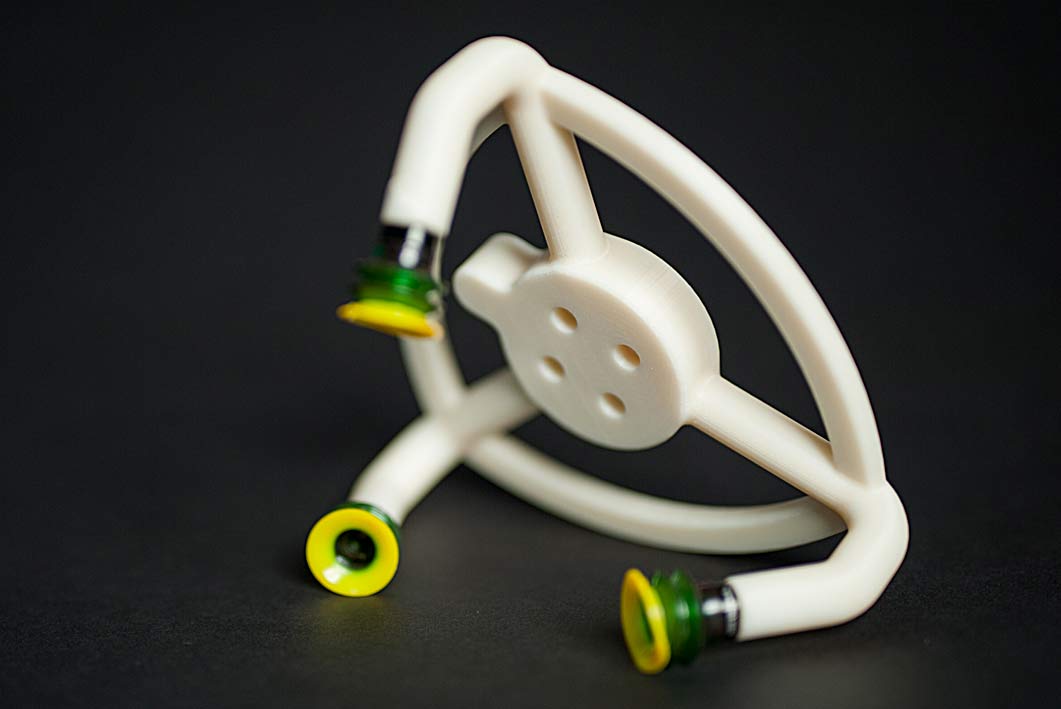
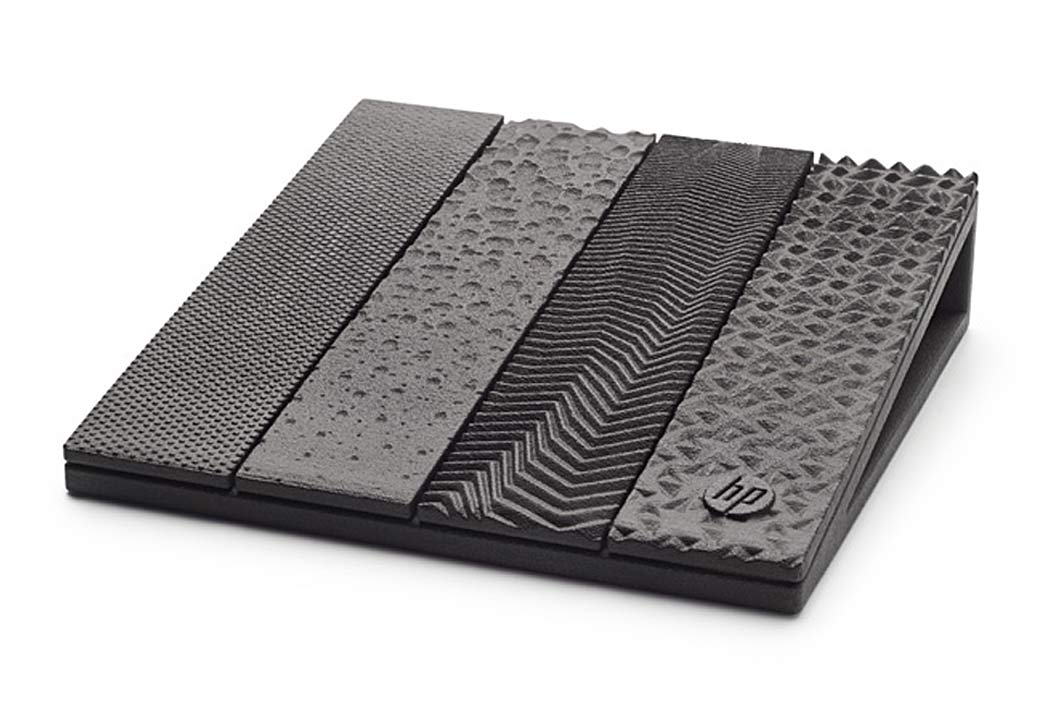
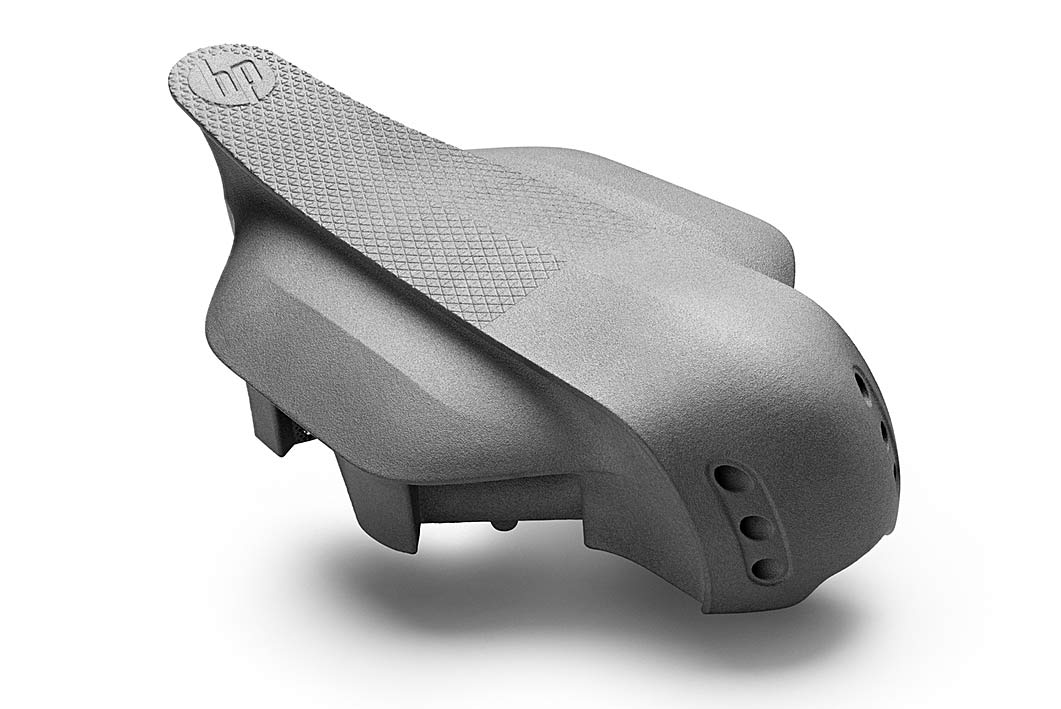
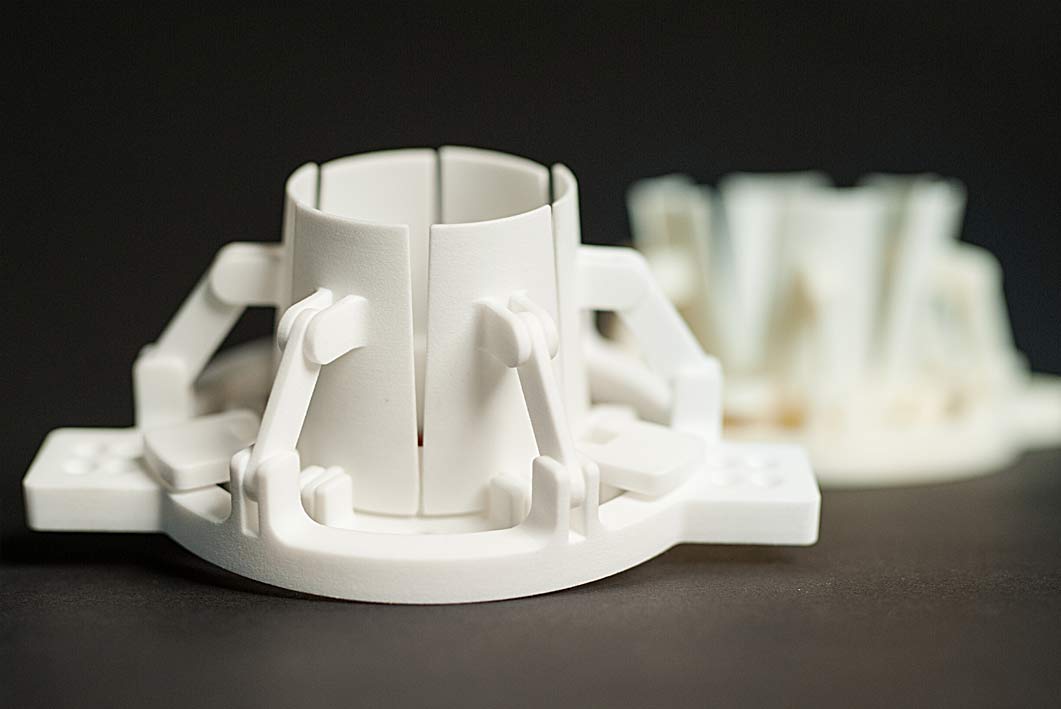
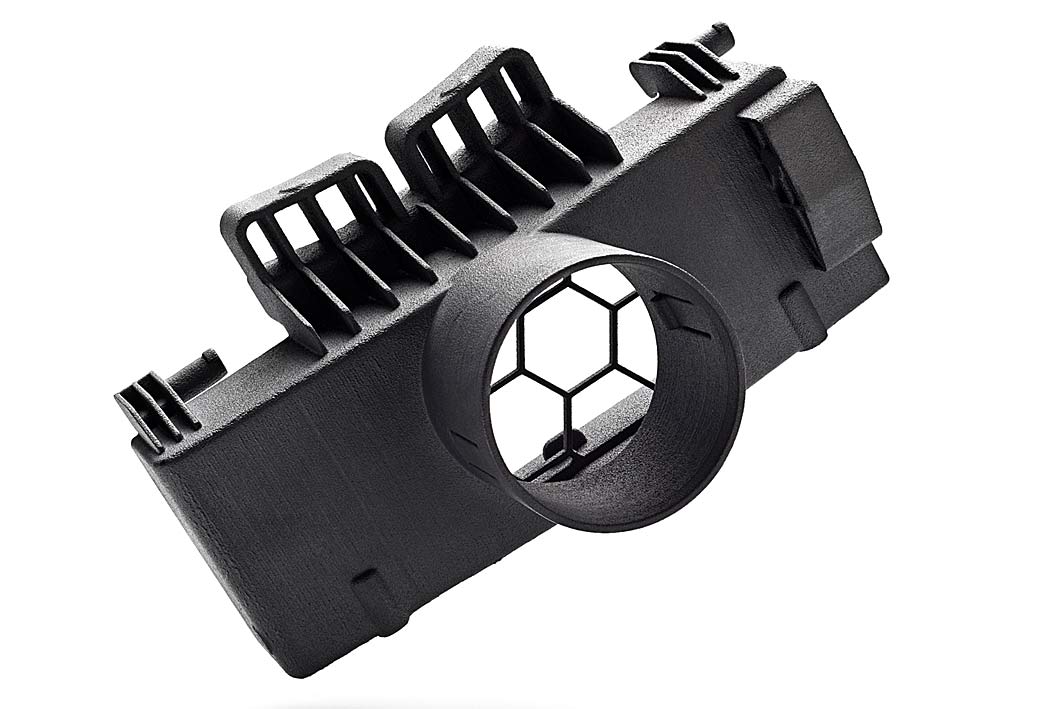